Lith Corporation, founded in 1998 by a group of material science doctor from Tsinghua University, has now become the leading manufacturer of battery lab&production equipment. Lith Corporation have production factories in shenzhen and xiamen of China.This allows for the possibility of providing high quality and low-cost precision machines for lab&production equipment,including: roller press, film coater,mixer, high-temperature furnace, glove box,and complete set of equipment for research of rechargeable battery materials. Simple to operate, low cost and commitment to our customers is our priority.
Nickel Foam (Ni Foam): A Comprehensive Overview
Nickel foam, often referred to as Ni foam, is a porous, lightweight material made from nickel metal. It is widely used in various industries due to its unique properties, including high porosity, excellent electrical conductivity, and mechanical stability. Nickel foam plays a critical role in applications such as energy storage, catalysis, filtration, and aerospace engineering.
Below is a detailed guide on nickel foam, including its structure, manufacturing process, properties, applications, and future trends.
●What Is Nickel Foam?
Nickel foam is a threedimensional, opencell structure composed of interconnected nickel struts or ligaments. The "foam" refers to its porous nature, which provides a large surface area relative to its volume. This structure makes nickel foam highly suitable for applications requiring efficient mass transfer, heat exchange, or electrochemical reactions.
Key characteristics:
High Porosity: Typically ranges from 70% to 98%, depending on the manufacturing process.
Uniform Pore Size: Pore sizes can range from micrometers to millimeters.
Mechanical Strength: Despite being lightweight, nickel foam exhibits good tensile and compressive strength.
Electrical Conductivity: Excellent conductivity makes it ideal for electrical and electrochemical applications.
●Manufacturing Process of Nickel Foam
The production of nickel foam involves several steps, depending on the desired properties and application. Below are the most common methods:
1. Powder Metallurgy
Step 1: Mix nickel powder with binders and other additives.
Step 2: Form the mixture into a green body using techniques like injection molding or extrusion.
Step 3: Sinter the green body at high temperatures (~1000°C) to fuse the particles while maintaining porosity.
2. Electroplating
Step 1: Use a sacrificial substrate (e.g., polyurethane foam) as a template.
Step 2: Deposit nickel onto the substrate through electroplating.
Step 3: Dissolve the substrate, leaving behind a porous nickel structure.
3. Replication Casting
Step 1: Create a mold using a porous material (e.g., ceramic or polymer).
Step 2: Fill the mold with molten nickel and allow it to solidify.
Step 3: Remove the mold, leaving behind a nickel foam replica.
4. Chemical Vapor Deposition (CVD)
Step 1: Expose a porous substrate to nickelcontaining gases (e.g., nickel carbonyl).
Step 2: Deposit nickel onto the substrate through chemical reactions.
Step 3: Remove the substrate if necessary.
5. Additive Manufacturing (3D Printing)
Recent advancements in additive manufacturing allow for the direct printing of nickel foam structures with precise control over pore size and geometry.
●Properties of Nickel Foam
| Property | Description |
|||
| Porosity | High (70–98%), providing a large surface area for reactions or filtration. |
| Density | Low (~1–5 g/cm³), making it lightweight yet strong. |
| Electrical Conductivity | Excellent (~1.4×10⁶ S/m), ideal for electrical and electrochemical applications. |
| Thermal Conductivity | Good (~90 W/m·K), enabling efficient heat dissipation. |
| Corrosion Resistance | Good resistance to corrosion in many environments, especially with protective coatings. |
| Mechanical Strength | High tensile and compressive strength, despite its porous structure. |
●Applications of Nickel Foam
1. Energy Storage
Battery Electrodes: Nickel foam is used as a current collector or scaffold for active materials in lithiumion batteries, supercapacitors, and fuel cells. Its high porosity allows for better electrolyte infiltration and improved ion transport.
Hydrogen Production: Used as a catalyst support in water electrolysis for hydrogen generation.
2. Catalysis
Nickel foam serves as a substrate for depositing catalytic materials (e.g., platinum, palladium) in chemical reactions such as hydrogenation, dehydrogenation, and reforming processes.
3. Filtration
Due to its uniform pore structure and mechanical strength, nickel foam is used in gas and liquid filtration systems, particularly in harsh environments where corrosion resistance is critical.
4. Aerospace and Automotive
Nickel foam is used in sound absorption, thermal insulation, and vibration damping in aerospace and automotive applications.
5. Medical Devices
In biomedical applications, nickel foam is used as a scaffold for tissue engineering or as a component in implantable devices.
6. Heat Exchangers
The high thermal conductivity and large surface area of nickel foam make it suitable for compact heat exchangers in industrial and electronic cooling systems.
Nickel Metal Foam
●Advantages of Nickel Foam
1. High Surface Area:
Enables efficient mass transfer, heat exchange, and electrochemical reactions.
2. Excellent Electrical Conductivity:
Ideal for battery electrodes, supercapacitors, and fuel cells.
3. Good Mechanical Properties:
Combines lightweight design with high strength and durability.
4. Corrosion Resistance:
Resistant to corrosion in many environments, especially when coated with protective layers.
5. Customizable Pore Structure:
Can be tailored for specific applications by adjusting pore size, shape, and distribution.
●Challenges in Nickel Foam
1. Cost:
Nickel foam can be expensive to produce, especially when using advanced manufacturing techniques like electroplating or 3D printing.
2. Brittleness:
While mechanically strong, nickel foam can be brittle under certain conditions, limiting its use in highstress applications.
3. Environmental Concerns:
Nickel is a heavy metal, and improper disposal of nickel foam can pose environmental risks.
4. Limited Scalability:
Some manufacturing processes, such as electroplating, may not be easily scalable for mass production.
●Future Trends in Nickel Foam
1. Additive Manufacturing:
Advances in 3D printing will enable the production of complex, customized nickel foam structures with precise control over pore size and geometry.
2. Advanced Coatings:
Development of protective coatings to enhance corrosion resistance and durability in harsh environments.
3. Composite Materials:
Integration of nickel foam with other materials (e.g., graphene, carbon nanotubes) to improve performance in energy storage and catalysis.
4. Sustainability:
Focus on environmentally friendly manufacturing processes and recycling strategies to reduce the ecological impact of nickel foam production.
5. New Applications:
Exploration of nickel foam in emerging fields such as quantum computing, advanced sensors, and renewable energy systems.
●Conclusion
Nickel foam is a versatile material with a wide range of applications in energy storage, catalysis, filtration, and more. Its unique combination of high porosity, excellent electrical conductivity, and mechanical strength makes it an indispensable component in modern technology. As advancements in manufacturing and materials science continue, nickel foam will play an increasingly important role in addressing global challenges related to energy, environment, and sustainability.
What aspect of nickel foam interests you most? Share your thoughts below! Together, let’s explore how this innovative material is shaping the future of advanced technologies.
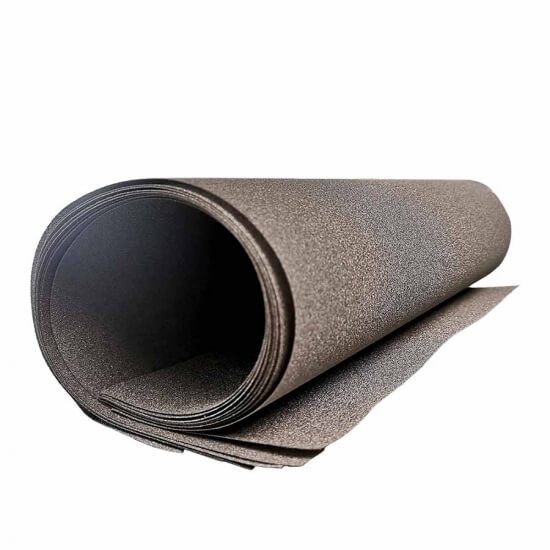